|
|
|
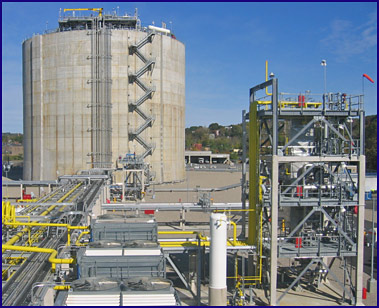 |
|
LGA Engineering is part of the owner's engineer team for an LNG peakshaving plant recently constructed in New England. Click picture for larger shots.
|
|
|
|
|
|
|
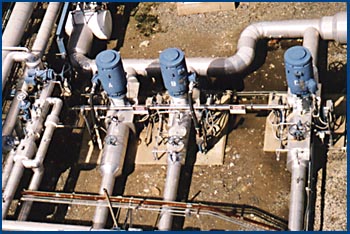 |
|
For a refrigerated LPG import terminal, LGA provided design and construction supervision for modification and expansion of pumping systems and LPG marine, rail, and truck loading facilities
|
|
|
|
|
|
|
|
For a leading vendor of selective catalytic reduction systems for reducing of nitrogen oxide emissions, LGA prepared general process equipment specifications for anhydrous ammonia unloading, storage, and transfer facilities for SCR installations to be located at coal fired power plants.
|
|
|
|
|
|
|
When an LPG import terminal added a second refrigerated storage tank, LGA handled expansion of the propane refrigeration system. In addition to the permanent system, we devised a means of using a rented chiller to provide essential refrigeration for continued plant operation during the switch. Click on the image to see the full process flow sheet for the temporary refrigeration system.
|
|
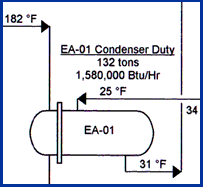 |
|
|
|
|
|
|
LGA served as process and mechanical design consultants to a pump service company for adapting an existing pump test circuit to be used for performance and acceptance testing of 1500 HP LNG hydraulic turbines.
|
|
|
|
|
|
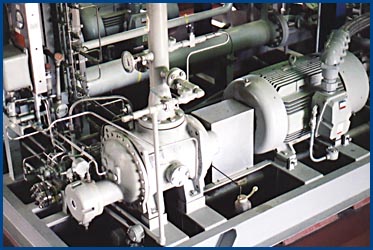 |
|
LGA Engineering was responsible for process equipment specifications and resolving design issues during refrigeration system upgrades for three refrigerated LPG terminals.
|
|
|
|
|
|
|
An LNG marine terminal operator used LGA Engineering for process evaluation, P&I diagrams, piping fabrication sketches, operating procedures, and safety analysis for use of transport trailer mounted LNG pumps to supply liquid for the gas trials of a gas ship returning to service.
|
|
|
|
|
|
|
|
|
|
|
|
Last Update 27 June 2008.
|
|
|
|
|
|
|
|
|
|
|
|
|
|
|
|
|
|
|
|